PVC Pipes Manufacturing Plant Project Report 2025: Manufacturing Plant Setup and Operations
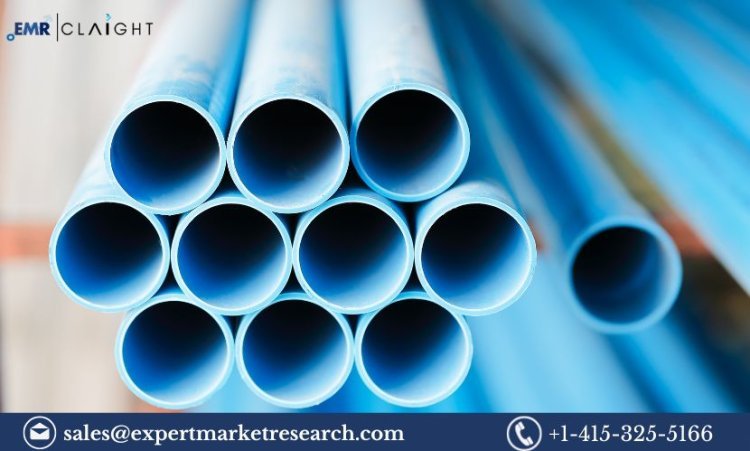
Introduction
Polyvinyl chloride (PVC) pipes are widely used across several industries, including construction, agriculture, telecommunications, and wastewater management. They are known for their durability, resistance to corrosion, lightweight nature, and ease of installation. PVC pipes are used for water supply, sewage systems, and cable insulation, among various other applications. The growing demand for infrastructure development, along with the increased focus on water conservation and management, has led to a steady rise in the demand for PVC pipes. This PVC Pipes Manufacturing Plant Project Report provides a detailed overview of the steps involved in setting up a manufacturing plant for PVC pipes. The report discusses the production process, raw materials, machinery, market analysis, financial considerations, and infrastructure requirements for a successful PVC pipe production unit.
Overview of PVC Pipes
Polyvinyl chloride, commonly known as PVC, is a synthetic polymer that is made from the polymerization of vinyl chloride. It is one of the most widely used plastics due to its versatility, cost-effectiveness, and ease of processing. PVC pipes are primarily used for the transport of water, gases, and sewage. The two primary categories of PVC pipes are rigid and flexible, with rigid pipes being the most common for plumbing and infrastructure applications.
Key Features of PVC Pipes:
- Durability: PVC pipes are highly durable, corrosion-resistant, and capable of withstanding harsh weather conditions, making them ideal for outdoor and underground use.
- Lightweight: They are much lighter compared to traditional metal pipes, which makes them easier to handle and install.
- Cost-Effective: PVC pipes are relatively inexpensive compared to alternatives such as copper or steel pipes.
- Versatility: PVC pipes are used in a wide range of applications including water supply, drainage systems, telecommunications, and electrical conduits.
- Low Maintenance: Due to their corrosion resistance, PVC pipes require minimal maintenance over their lifespan.
The demand for PVC pipes has seen steady growth due to urbanization, the need for reliable infrastructure, and advancements in plumbing systems.
Get a Free Sample Report with Table of Contents@
Manufacturing Process of PVC Pipes
The process of manufacturing PVC pipes involves the extrusion of PVC resin, which is then shaped into pipe form. The manufacturing process is highly automated and consists of several key steps to ensure the production of high-quality PVC pipes.
1. Preparation of Raw Materials
The main raw materials used in PVC pipe production include:
- PVC Resin: The base material for PVC pipe production. It is available in the form of fine powder and is the key ingredient in the extrusion process.
- Stabilizers and Additives: These are added to the PVC resin to enhance the pipe’s properties such as UV resistance, impact resistance, and flexibility.
- Plasticizers: Used in flexible PVC pipes to improve flexibility.
- Lubricants: Added to reduce friction during the extrusion process and improve the flow of the material.
2. Compounding
In the compounding process, the PVC resin is mixed with stabilizers, additives, plasticizers, and lubricants to form a uniform compound. This step is crucial for ensuring that the PVC pipes will have the required characteristics such as strength, durability, and flexibility. The compounding process is typically carried out in an industrial mixer or extruder.
3. Extrusion Process
The compounded PVC material is fed into an extruder, which heats the material to a specific temperature and forces it through a die to form the pipe shape. The extruder is equipped with a screw mechanism that melts the PVC material and shapes it into the desired pipe size.
- Heating: The PVC compound is heated to approximately 180-200°C (356-392°F) to make it soft and moldable.
- Extrusion: The heated material is pushed through a mold (die) to form the pipe. The shape of the die determines the diameter and thickness of the pipe.
- Cooling: After the extrusion process, the hot PVC pipe is cooled using a water bath or air-cooling system to solidify the material.
4. Sizing and Calibration
After the extrusion process, the pipe undergoes sizing and calibration. This step ensures that the pipe has the correct diameter and wall thickness. The pipe is passed through a sizing sleeve or vacuum tank to maintain its shape and size while cooling.
5. Cutting
Once the PVC pipe has cooled and is properly sized, it is cut into desired lengths, which are typically 6 meters or 12 meters, depending on the customer’s specifications. The cutting is done using automated saws that provide precise lengths with minimal material loss.
6. Inspection and Quality Control
Before the pipes are packaged, they undergo a series of quality control tests. These tests may include:
- Dimensional Inspection: To check if the pipe’s diameter and wall thickness meet the required specifications.
- Impact Testing: To evaluate the pipe’s resistance to breakage under pressure.
- Hydrostatic Testing: To test the pressure endurance of the pipe.
Only pipes that meet the required quality standards are sent for packaging.
7. Packaging
After passing the quality control checks, the PVC pipes are packaged and prepared for shipment. The pipes are typically bundled in units of 10-50 pipes per bundle, depending on the size and customer requirements. The packaging ensures the pipes are protected from damage during transportation and storage.
Raw Materials and Inputs Required
The main raw materials required for the production of PVC pipes include:
- PVC Resin: The base material for manufacturing PVC pipes.
- Additives and Stabilizers: Chemicals such as stabilizers, plasticizers, lubricants, and UV protectants are used to enhance the properties of the pipes.
- Energy: Electricity is required for running extrusion machines, cooling systems, and other machinery.
- Water: Water is used for cooling and washing the pipes during the manufacturing process.
- Packaging Materials: Packaging materials such as plastic shrink wrap, stretch film, and wooden pallets for shipping and handling.
Machinery and Infrastructure Requirements
Setting up a PVC pipe manufacturing plant requires a variety of specialized machinery and infrastructure:
Machinery:
- Extruder: The primary machine used for the extrusion of PVC material into pipe form.
- Molds and Dies: Custom molds and dies are required to shape the PVC into the desired pipe size and thickness.
- Cooling Tanks: Used to cool the extruded pipes and solidify the material.
- Cutting Machines: Automated cutting machines for precisely cutting the pipes into desired lengths.
- Sizing and Calibration Equipment: Equipment to maintain the correct diameter and wall thickness.
- Testing and Inspection Equipment: Tools and machinery for quality control and testing the physical properties of the pipes.
Infrastructure:
- Factory Building: A well-ventilated and spacious production facility that can accommodate all the machinery and provide ample space for storage.
- Water Supply System: A reliable water supply is essential for cooling the pipes during the manufacturing process.
- Power Supply: A stable electricity supply is required to run the heavy machinery and ensure smooth production.
- Storage and Packaging Area: Adequate space for storing raw materials, finished products, and packaging materials.
Financial Considerations
Initial Investment
The initial investment required for establishing a PVC pipe manufacturing plant includes the following:
- Land and Building: Costs related to purchasing land and constructing the factory building.
- Machinery and Equipment: Purchase of extrusion machines, molds, cutting machines, cooling systems, and testing equipment.
- Raw Materials: Initial procurement of PVC resin, stabilizers, additives, and other materials required for production.
- Licensing and Permits: Costs for obtaining necessary licenses and permits from local authorities and regulatory bodies.
- Working Capital: Funds required for operational expenses such as labor, utilities, and raw material procurement.
Operating Costs
The operating costs for a PVC pipe manufacturing plant include:
- Raw Material Costs: Continuous purchase of PVC resin, stabilizers, plasticizers, and other additives.
- Labor Costs: Salaries for factory workers, engineers, and administrative staff.
- Energy Costs: Electricity and fuel for running the production machinery and maintaining the factory environment.
- Maintenance Costs: Regular maintenance of machinery and plant infrastructure.
- Packaging and Distribution Costs: Costs associated with packaging the pipes and distributing them to customers.
Revenue Generation
Revenue is generated through the sale of PVC pipes to various industries, including construction, irrigation, and plumbing. The pricing of PVC pipes is determined based on factors such as diameter, wall thickness, and the quantity purchased by customers.
Market Analysis and Demand Forecast
The demand for PVC pipes is growing, driven by various factors such as:
- Urbanization: As urban areas expand, there is an increased need for plumbing, water supply systems, and sewerage networks.
- Agricultural Development: PVC pipes are widely used in irrigation systems, contributing to agricultural productivity.
- Infrastructure Development: Governments and private sector players are investing in infrastructure projects, creating a high demand for reliable piping solutions.
The global market for PVC pipes is expected to continue growing in the coming years, with the construction and agricultural sectors leading the demand.
Regulatory Compliance and Certifications
To operate a PVC pipe manufacturing plant, manufacturers must adhere to various regulatory standards to ensure product quality and safety. Key certifications include:
- ISO 9001: Quality management certification to ensure consistent product quality.
- ISO 14001: Environmental management certification to ensure that the manufacturing process does not negatively impact the environment.
- ASTM Standards: Compliance with standards set by the American Society for Testing and Materials (ASTM) for PVC pipes.
Media Contact
Company Name: Claight Corporatio
Contact Person: Lewis Fernandas, Corporate Sales Specialist — U.S.A.
Email: sales@expertmarketresearch.com
Toll Free Number: +1–415–325–5166 | +44–702–402–5790
Address: 30 North Gould Street, Sheridan, WY 82801, USA
Website: www.expertmarketresearch.com
Aus Site: https://www.expertmarketresearch.com.au
What's Your Reaction?






