Aluminium Wire Drawing Manufacturing Plant Project Report 2025: Project Report and Insights
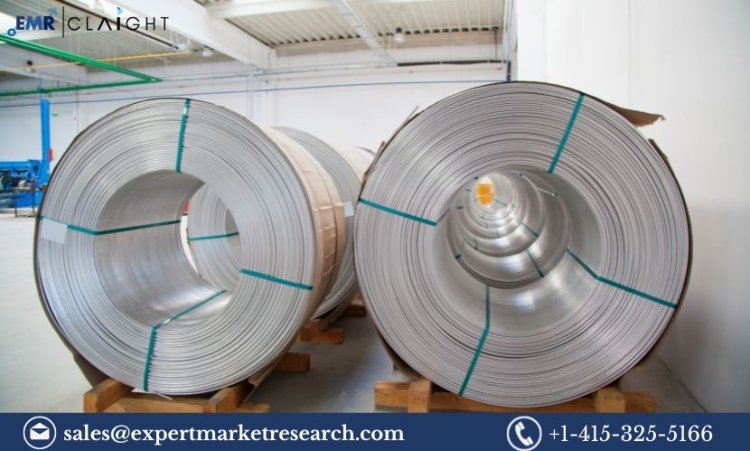
Introduction
The Aluminium Wire Drawing Manufacturing Plant Project Report is an ambitious industrial venture aimed at producing high-quality aluminium wires through a specialized process known as wire drawing. Aluminium wire drawing is an essential procedure in various industries, from electrical and automotive to construction and electronics. With the growing demand for lightweight, durable, and corrosion-resistant materials, aluminium has emerged as one of the most preferred metals. This article will delve into the details of setting up an aluminium wire drawing manufacturing plant, the processes involved, and the benefits of investing in such a project. By the end of this guide, you’ll have a comprehensive understanding of how to establish a successful aluminium wire drawing manufacturing plant.
What is Aluminium Wire Drawing?
Aluminium wire drawing is a mechanical process that involves reducing the diameter of an aluminium rod or billet by pulling it through a series of progressively smaller dies. The purpose of this process is to produce wires with a desired diameter, which are then used for various applications like electrical wiring, telecommunications cables, and more. Wire drawing helps improve the tensile strength and surface finish of the wire, making it more suitable for diverse applications.
This manufacturing process is highly versatile and can be adapted to create wires of various dimensions and specifications. The main advantage of aluminium wire is its lightweight nature, excellent electrical conductivity, and resistance to corrosion, making it an ideal material for industries that require efficient and durable wire products.
Key Components of an Aluminium Wire Drawing Manufacturing Plant
1. Raw Material Procurement
The first step in setting up an aluminium wire drawing plant is securing a reliable supply of raw aluminium. Typically, aluminium wire drawing begins with casting billets or rods, which are the starting material for wire production. These billets are typically sourced from aluminium ingots or scrap materials. Establishing strong relationships with suppliers is crucial to ensure a consistent and high-quality supply of aluminium.
2. Wire Drawing Machine
The core of any aluminium wire drawing manufacturing plant is the wire drawing machine. These machines consist of a set of dies through which the aluminium billets are pulled to reduce their diameter. Some common types of wire drawing machines include single-die and multi-die machines, depending on the required output and wire dimensions.
In addition to the basic drawing machine, there are various ancillary components, such as lubricating systems to reduce friction, cooling systems to manage the heat generated during the process, and tension controls to maintain the desired drawing speed.
Get a Free Sample Report with Table of Contents@
3. Annealing Furnace
After the aluminium is drawn to the desired diameter, it typically undergoes a process called annealing. Annealing involves heating the wire to a specific temperature and then cooling it slowly to soften the material. This improves the wire’s ductility, making it easier to handle and use in various applications. The annealing furnace is a critical component of the plant, as it ensures the final wire product has the required mechanical properties.
4. Coiling and Packaging Units
Once the wire is drawn and annealed, it is coiled into spools or reels for easy handling, storage, and transportation. This step involves automated systems that wind the wire into consistent coils to ensure smooth operation in later stages of the manufacturing process. Packaging units are also essential for labeling, quality control, and preparing the wire for shipment to customers.
5. Quality Control and Testing Equipment
To ensure that the aluminium wire meets the required specifications and quality standards, a well-equipped quality control (QC) lab is necessary. The QC department will test the wires for characteristics such as tensile strength, elongation, surface finish, and electrical conductivity. High-quality testing equipment ensures that only the best products are sent to customers, which is essential for maintaining customer satisfaction and meeting industry standards.
Major Considerations Before Starting the Plant
1. Market Research and Demand Analysis
Before embarking on an aluminium wire drawing manufacturing plant project, extensive market research is crucial. Understanding the demand for aluminium wire in different industries is vital to ensure the plant will be financially viable. The wire manufacturing industry serves diverse sectors such as electrical, telecommunications, automotive, and construction. Conducting a thorough demand analysis will help you determine the plant's production capacity, product types, and pricing strategies.
2. Location and Infrastructure
Selecting the right location for the plant is a critical decision. Factors such as proximity to raw material suppliers, access to transportation networks, availability of skilled labor, and government policies will influence the decision. The plant should be situated in a location where it can easily access resources while maintaining low production and transportation costs.
Additionally, the plant’s infrastructure must support the heavy machinery used in wire drawing. Adequate power supply, water resources, and waste management systems are essential to ensuring smooth operations.
3. Initial Investment and Cost Analysis
The capital investment required for establishing an aluminium wire drawing manufacturing plant can be substantial. This includes the cost of purchasing machinery, raw materials, setting up infrastructure, hiring staff, and ensuring compliance with environmental and safety regulations. A detailed cost analysis will help determine the total project cost and establish a realistic timeline for return on investment (ROI).
4. Compliance with Industry Standards
Aluminium wire drawing plants must comply with a variety of industry standards, ranging from environmental regulations to safety protocols. Adherence to international standards such as ISO, ASTM, and IEC is crucial for maintaining the quality and safety of products. Additionally, environmental impact assessments should be conducted to minimize the ecological footprint of the manufacturing process, including the proper disposal of waste products.
The Process of Aluminium Wire Drawing
1. Pre-drawing Preparation
Before the wire drawing process begins, the raw aluminium billets or rods are cleaned and preheated to prepare them for drawing. This step helps remove any impurities on the surface of the material and reduces the risk of surface defects during the drawing process.
2. Wire Drawing
The wire drawing process is carried out by passing the aluminium billets through a series of dies that progressively reduce their diameter. This step can be done in multiple stages depending on the desired size and properties of the finished wire. In each stage, the wire is drawn through smaller and smaller dies until it reaches the final dimension.
During the drawing process, the wire is subjected to high levels of tension, which can generate significant heat. To mitigate this, the wire is lubricated to reduce friction, and cooling systems are employed to manage the heat.
3. Annealing
After the wire has been drawn to the desired size, it is typically passed through an annealing furnace. The wire is heated to a high temperature and then slowly cooled to relieve internal stresses, increase ductility, and improve overall mechanical properties. Annealing is essential to ensure the wire is pliable and suitable for further processing or use in various applications.
4. Post-drawing Processing
After annealing, the wire undergoes additional processes, including winding onto spools or coils and applying surface coatings if required. The wires are then inspected for any defects, such as surface cracks, bends, or inconsistencies in diameter. Quality control checks ensure that the final product meets the required standards for strength, flexibility, and surface finish.
5. Packaging and Shipping
Once the aluminium wire is produced and passes all quality checks, it is carefully packaged and prepared for shipment. Packaging typically includes labeling with specifications, such as wire gauge, length, and material composition, so customers can easily identify the product. The wires are then shipped to customers in various industries such as construction, automotive, and telecommunications.
Challenges in Aluminium Wire Drawing Manufacturing
While the process of setting up and operating an aluminium wire drawing manufacturing plant can be rewarding, several challenges must be considered:
1. Energy Consumption
The aluminium wire drawing process requires substantial energy, especially during the drawing and annealing stages. Energy-efficient technologies can help reduce energy consumption, but it is essential to consider the impact of energy costs on overall profitability.
2. Material Waste
Waste generation is another concern in wire drawing. Although the aluminium wire drawing process is highly efficient, there will inevitably be some material waste during drawing, cutting, and coiling. Finding ways to reduce waste and recycle scrap material is essential for minimizing environmental impact and reducing production costs.
3. Technological Advancements
Staying up-to-date with technological advancements is crucial in the aluminium wire drawing industry. Advancements in automation, quality control systems, and energy-efficient equipment can significantly improve production efficiency and product quality. However, keeping pace with new technologies requires ongoing investment in research and development.
4. Market Competition
The aluminium wire industry is competitive, with numerous manufacturers worldwide. To stay ahead of the competition, it is essential to maintain high-quality production standards, offer competitive pricing, and invest in innovation. Establishing a strong brand presence and customer relationships will also help secure a place in the market.
Media Contact
Company Name: Claight Corporation
Contact Person: Peter Fernandas, Corporate Sales Specialist — U.S.A.
Email: sales@expertmarketresearch.com
Toll Free Number: +1–415–325–5166 | +44–702–402–5790
Address: 30 North Gould Street, Sheridan, WY 82801, USA
Website: www.expertmarketresearch.com
Aus Site: https://www.expertmarketresearch.com.au
What's Your Reaction?






